Positioning and scope of application of the three standards
1.API 594
Core Positioning: Specifically for the design and manufacture of butt-clamp (Wafer) and double-flanged (Lug) check valves.
Typical applications:
High-pressure, high-frequency start/stop pipework (e.g. pump outlets).
Compact installations where space is limited.
Severe working conditions where backflow of media has to be prevented.
2.API 6D
Core Positioning: For pipeline valves, including ball valves, gate valves, check valves and plug valves.
Typical applications:
Long-distance oil and gas pipelines (e.g. crude oil, natural gas trunk lines).
Large diameter and high pressure rating valve requirements.
3.API 602
Core Positioning: for compact gate, globe, and check valves (Bore typically ≤ NPS 4, Pressure Rating ≤ Class 1500).
Typical applications:
Fine control systems for small bore, high pressure and high temperature.
Volume sensitive applications such as refineries and wellhead equipment.
Comparison of key differences
Comparison Dimension |
API 594 |
API 6D |
API 602 |
Applicable Valve Type |
For Wafer/Double Flange Check Valves Only |
Various valves (ball valves, gate valves, etc.) |
Compact Gate, Globe, Check Valves |
Size range |
Normally NPS 2~24 |
Large calibre predominant |
Small Diameter (≤NPS 4) |
Pressure rating |
Class 150~2500 |
Class 150~2500 |
Class 150~1500 |
Test Requirements |
Bi-directional seal test (prevents backflow) |
One-way seals are predominant |
High Pressure Gas Seal Testing |
Structural Characteristics |
Lightweight and reliant on pipe bolting |
Individual Flange Connections for Long Pipelines |
Short Structure, Integrated Valve Body Design |
Suggestions for selection: matching criteria according to scenarios
1.Typical scenarios for selecting API 594
Pump outlet protection: need to close quickly to prevent water hammer effect, and limited installation space.
Chemical plant: the medium is highly corrosive, requiring two-way zero-leakage sealing.
Advantages: light weight, low flow resistance, strong impact resistance.
2.Typical scenarios for choosing API 6D
Long-distance oil and gas pipeline: need large diameter, high pressure capacity of the valve (such as ball valves).
Trunk line isolation: requires valves to be installed independently and support pipe cleaning operations.
3.Typical scenarios for selecting API 602
High-pressure, small-diameter systems: such as refinery instrument air piping, wellhead control valve manifolds.
High temperature steam systems: short structure design to reduce the effects of thermal expansion.
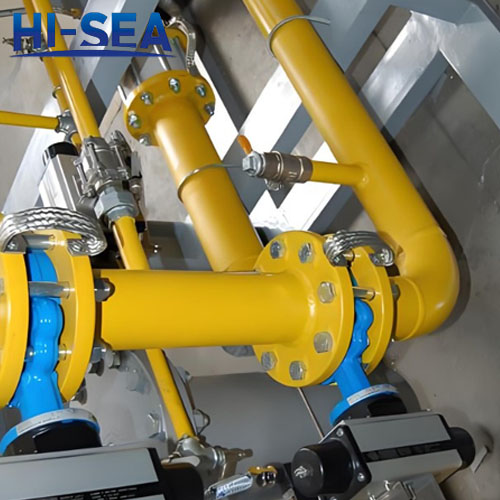